Partiamo dalla calotta esterna.
La sua funzione principale non è assorbire l’energia creata dall’impatto, ma cercare di distribuirla su tutta la superficie, in modo da proteggere anche gli altri componenti interni. Può essere costruita con fibre composite o con materie plastiche.
Quali sono le differenze? La calotta in fibre composite (fibre di vetro, Kevlar, dyneema, carbonio) può essere realizzata in mono composito (solo con fibre di vetro) oppure mescolando fibre di vetro con le altre.
Successivamente queste fibre vengono amalgamate fra loro con delle speciali resine termoindurenti per renderle solide e resistenti. Invece per stampare una calotta in materie plastiche si usano il policarbonato – migliore a livello di assorbimento degli urti – e l’ABS (acronimo di acrilonitrile, butadiene e stirene, tre monomeri di base). È più soggetta agli sbalzi di temperatura rispetto alla calotta in fibre composite, ma non per questo meno sicura.
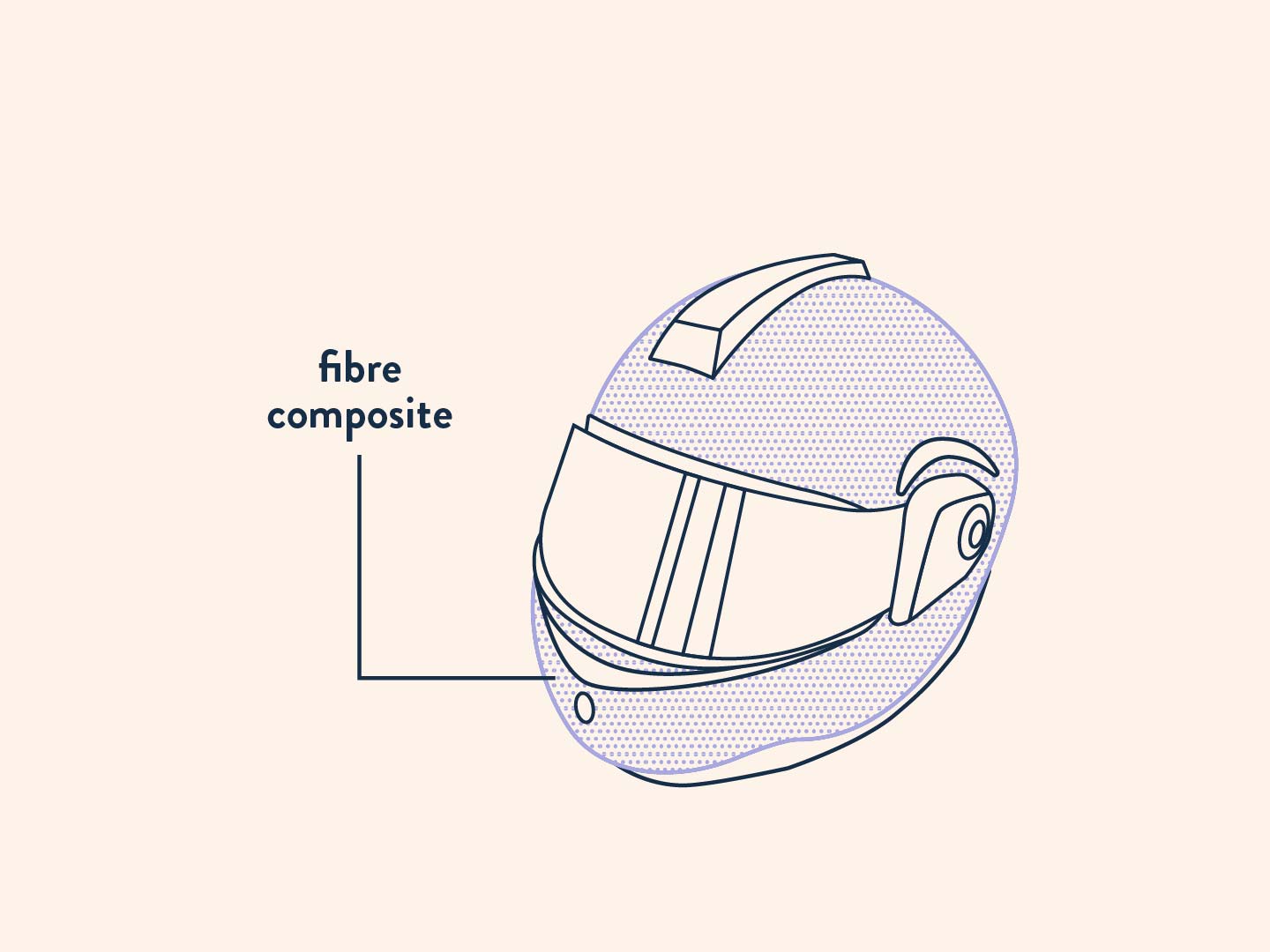
La calotta interna potrebbe essere considerata un po’ come l’anima del casco. Viene stampata in polimeri espansi ed è l’unico componente del casco in grado di assorbire energia. Durante una caduta o un incidente è in grado di deformarsi, in modo da disperdere la forza dell’impatto, per garantire massima protezione alla testa.
Ogni calotta interna che si rispetti viene stampata in varie densità, così da potersi sposare perfettamente con la calotta esterna: a seconda del materiale con cui è costruita, sarà associato un polistirolo più o meno consono. Ad esempio, se la calotta esterna è fatta in carbonio (quindi molto resistente e rigida) verrà usata una calotta interna di densità bassa, più morbida.
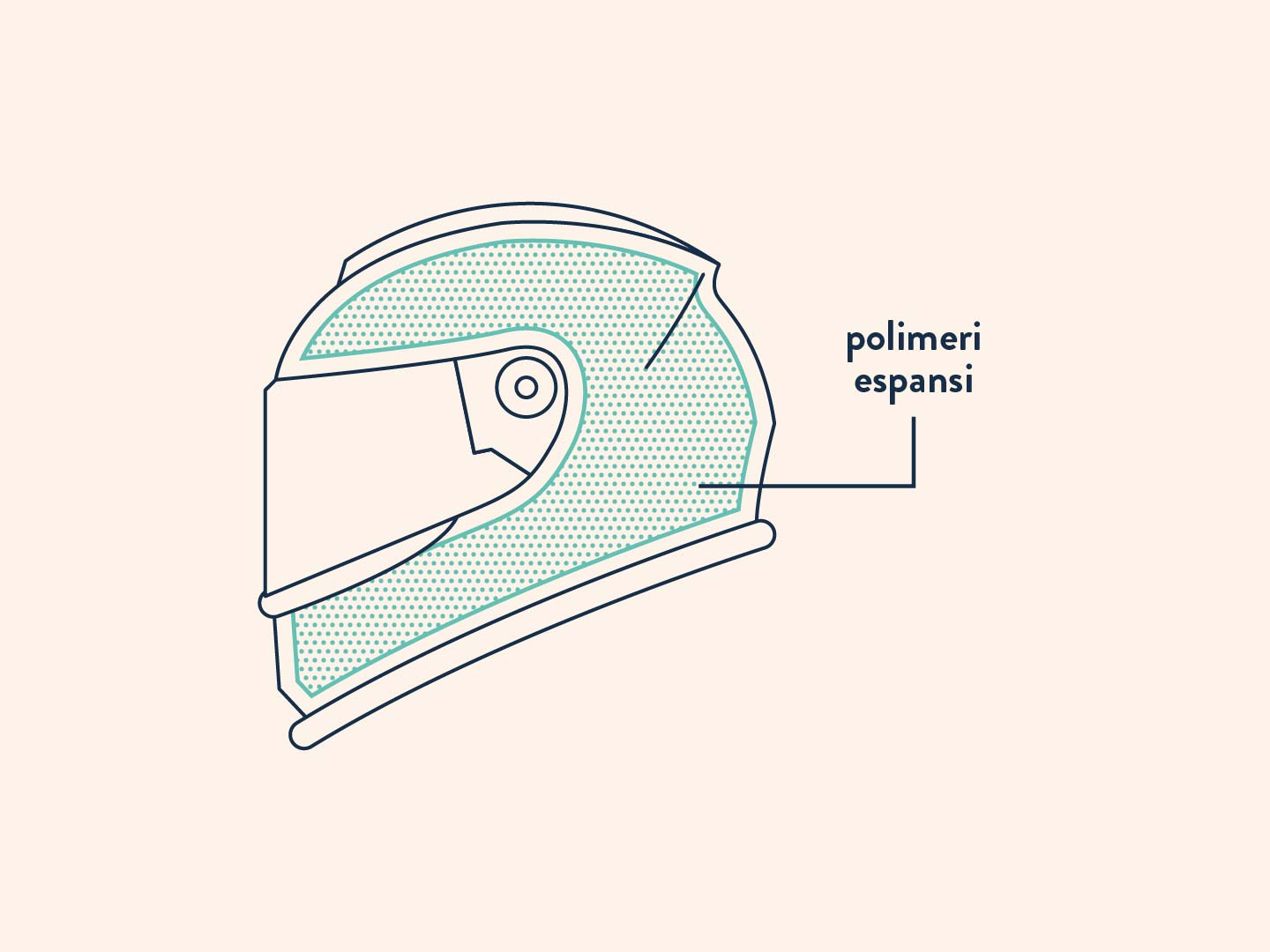
La visiera di un casco moto può essere prodotta in stampo, iniettando il policarbonato trasparente all’interno di uno stampo di acciaio, oppure in termoformatura (una tecnica di stampaggio di materie plastiche a caldo), tranciando una lastra secondo la forma che si vuole dare alla visiera e poi termoformandola successivamente per ottenere la giusta curvatura. Lo spessore di una visiera comunemente usata varia dai 2 ai 3 millimetri e deve essere resistente all’abrasione e agli urti.
Si ringrazia il Professor Maurizio Masi, Dipartimento di Chimica, Materiali e Ingegneria chimica “Giulio Natta” del Politecnico di Milano
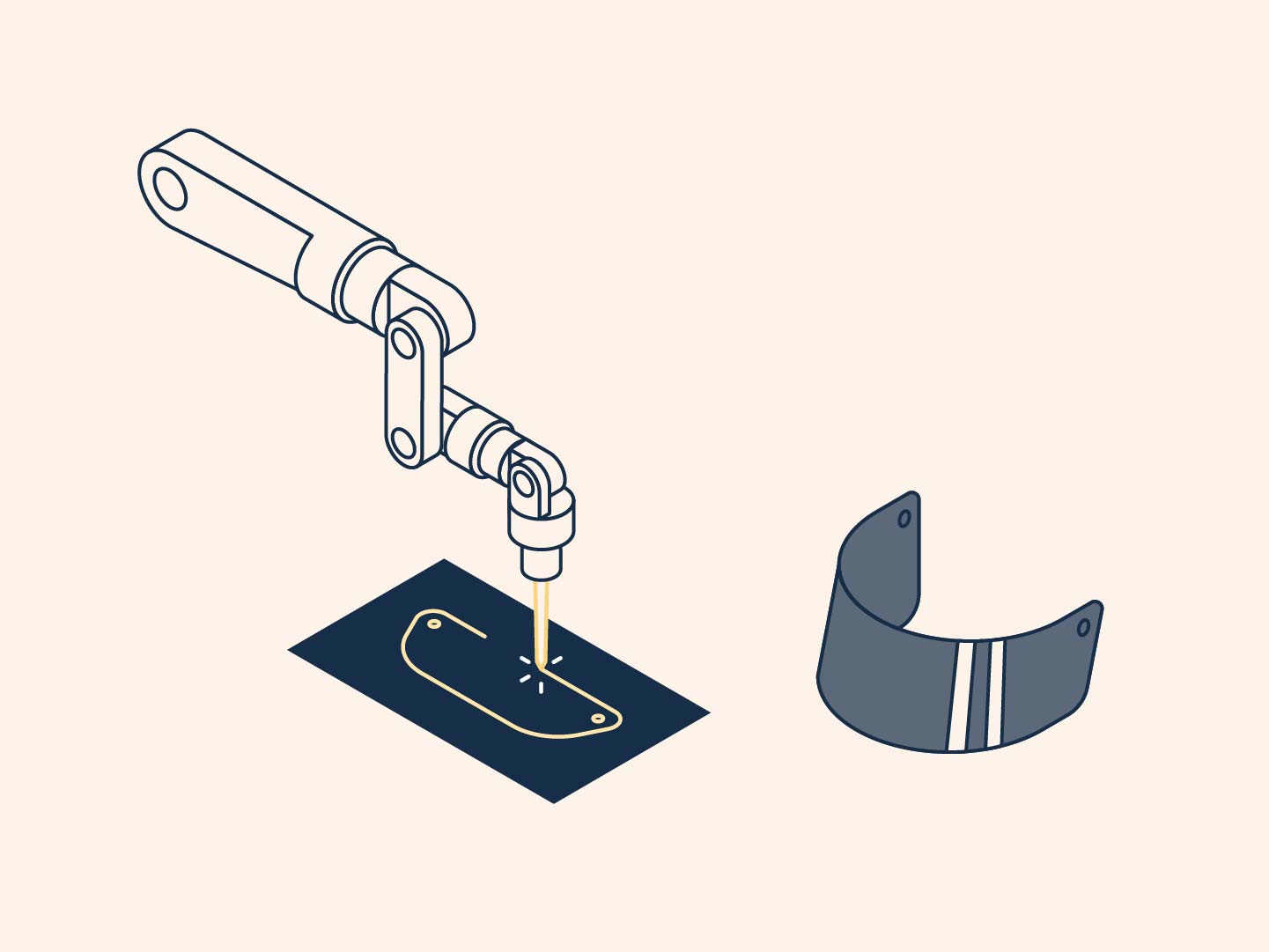